Executive Summary
The project was to build a residential two storey building, housing ten one-bedroom apartments constructed using sustainable material in Austria and then delivered, prefabricated, to the UK. A CLT frame building was the method of choice. CLT, Close-Laminated Timber, builds are used for prefabricated structures as an alternative to traditional concrete and steel. They are made using layers of timber glued together alternating at 90-degree angles for each layer and are commonly used as load-bearing walls and fixed in position to make a closed plan design.
The time-frame of this construction was far quicker than traditional builds. It was installed within a few weeks compared to conventional builds of several months. Having a CLT build also allows for exterior and interior finishes to be completed simultaneously saving time and money.
Challenges
The main challenge for this project was coordination and communication. It was vital that all parties involved were well informed and each individual was coordinated to come together to execute a successful build.
The CLT frame was designed and engineered off-site, including all openings and service routing, to allow for structural stability of all apertures. It was crucial that the design team, such as the Architect and Mechanical Engineers, established and set the parameters of the design in the early stages of the process.
The frame production was then fabricated off-site and Installed on-site. Therefore, the need for cutting or changes were kept to a minimum once on-site.
Secondary fixings would be made to the face of the frame rather than the integral frame. Analysis of the design was carried out to check if secondary penetration was viable without destabilizing the frame core structure.
The nature of CLT frames means they are bulky. The frame was delivered to site via an articulated vehicle which can cause challenges if not taken into consideration. The need for clear access and accessible roads was fundamental. Then the frame was craned from the vehicle to location, so an on-site mobile crane unit was needed. The frame was then lifted into its allocated slots or nodes then secured using an ‘air fix’ method.
Whilst this work was being carried out all contractors were expected to keep clear due to safety, therefore their individual works were halted until safe to resume. However, the speed of assembly mitigated the delay by enabling contractors to complete their works.
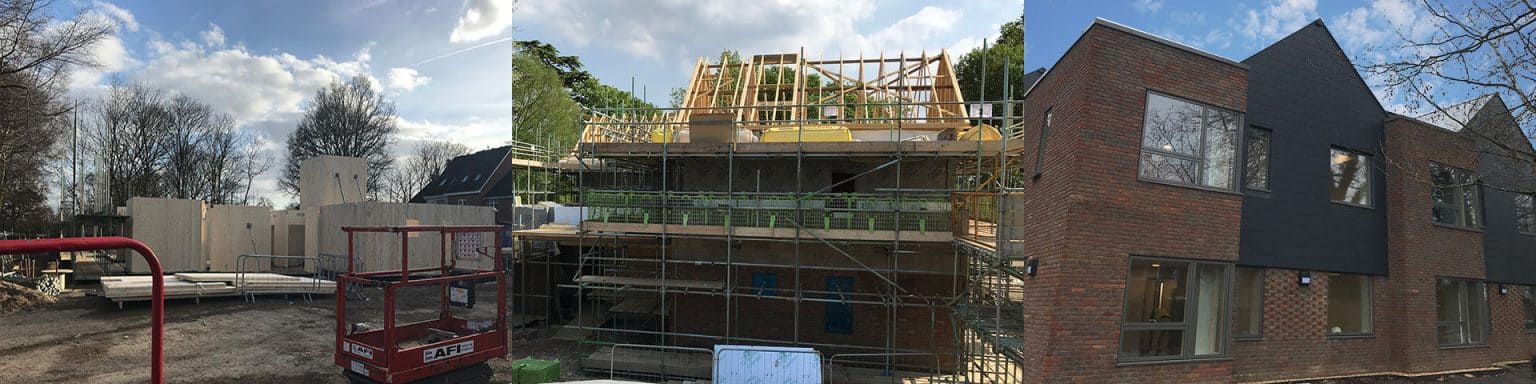
The Solution
The build was highly successful and constructed in a significantly shorter period of time from design to erection compared to traditional methods. The client was able to go to market sooner than planned.
Syndicate Group Southern’s experience and understanding of the complexities of this build ensured a thorough analysis was executed with the consulting team. It was critical that the planning was reviewed and verified that the build had the capacity to work.
The Result
CLT builds are very versatile and have multiple benefits.
Costs are managed and controlled due to the pre-set design and prefabricated build upfront before any construction is executed on-site.
The speed of erection is significantly faster than traditional builds for the same site area. This leads to waterproofing the building much sooner in the process and finishes completed earlier.
CLT builds also help with the reduction in carbon footprint. By using sustainable wood instead of concrete, Co2 emissions are hugely reduced due to sequestered carbon that is stored naturally in the trees that are used for the timber. CLT builds also benefit from enhanced thermal and air tightness performance making the build more energy efficient.
CLT builds are therefore an ideal solution for low rise buildings if you want to avoid using concrete and steel. Syndicate Group Southern have the professional knowledge and experience to offer an exceptional solution in this discipline whether it is for residential, commercial or some other innovative concept.